The Critical Role of the Coal Dust Explosion Test in Industrial Safety
Coal dust poses a serious threat in many industries. Because it is so fine, it quickly becomes airborne, making it easy to ignite and cause explosions. This issue is particularly common in factories and mines.
Throughout history, coal dust explosions have caused enormous destruction, leveling buildings and claiming many lives. Some of the worst industrial disasters were triggered by coal dust, highlighting its dangerous potential.
To maintain safety, companies must take action before accidents happen. Regular testing of coal dust is a crucial step, as it allows for early detection of potential risks. But how can we test coal dust in a way that ensures everyone’s safety?
Understanding Coal Dust Explosions
Coal Dust as a Safety Hazard
Coal dust is a serious danger in coal mines and processing plants. It spreads in the air and can catch fire easily. When it burns in a closed space, like a mine tunnel or coal storage bin, it creates a strong blast. This explosion can break structures and cause harm to workers. Many accidents have happened because of coal dust. It is important to control this risk before it leads to disaster.
Testing for Explosion Risks
To know if a workplace has a dust explosion risk, companies must do tests. These tests check how easily coal dust can explode. Experts use special methods to study coal dust dangers. Some important testing standards are:
- ISO/IEC 80079-20-2-2016 – Tests for combustible dust in explosive atmospheres
- VDI 2263.1-1990 – Measures dust safety characteristics
- ASTM E 1226-2012a – Checks dust cloud explosibility
- GB/T 3836.12-2019 – Studies combustible dust properties
The Coal Dust Explosion Test is one way to see how likely coal dust is to explode under different conditions.
Reliable Testing Equipment
Zeal Instruments makes tools for dust explosion testing. These tools help measure how dangerous coal dust can be. They check explosion power and safety limits. Companies use this data to make better safety plans. Good testing helps reduce accidents and keeps workplaces safe.
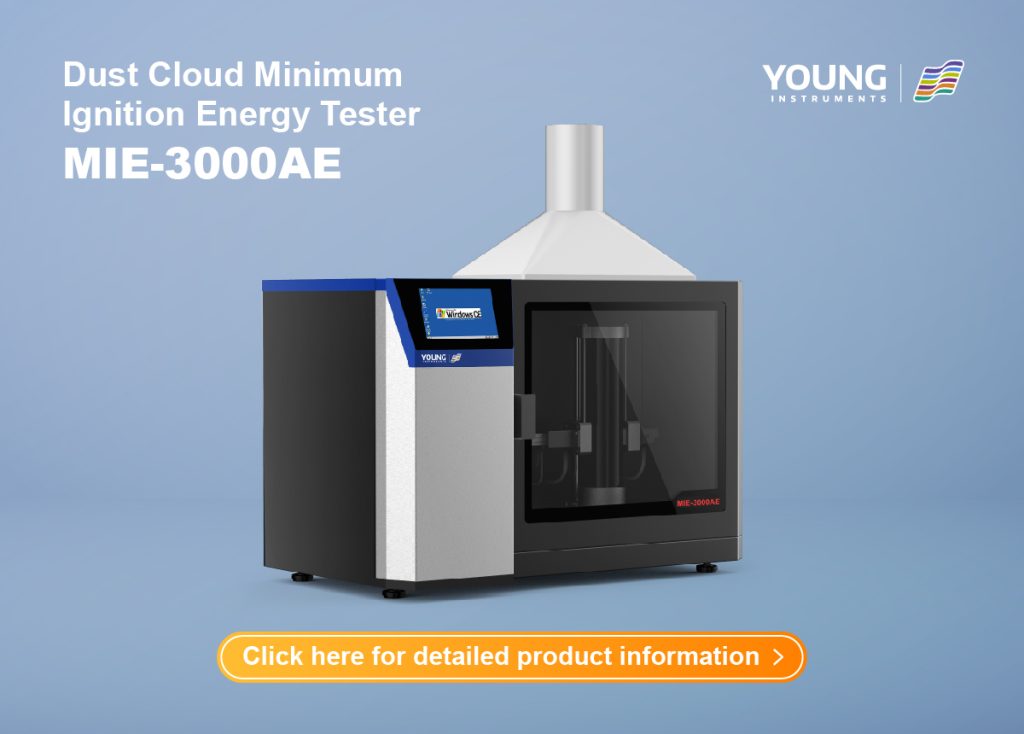
MIE-3000AE: Advanced Dust Cloud Ignition Testing
How It Works
The MIE-3000AE measures the Minimum Ignition Energy (MIE) of dust clouds. It uses compressed air to disperse dust into a 1.2L Hartmann tube, followed by a controlled spark to ignite the cloud. The device identifies the lowest ignition energy required by running multiple tests. This helps industries assess the fire risk of dust clouds, providing crucial data for explosion risk management.
Key Features for Safety and Accuracy
The MIE-3000AE adheres to international standards and allows for both standard and custom testing modes. It supports spark energy settings from 1mJ to 3000mJ, adjustable in 1mJ steps. Users can modify electrode distance (2mm to 10mm), powder pressure (0.4MPa to 0.7MPa), and ignition delay (20ms to 180ms). A high-voltage relay trigger and moving electrode trigger enhance precision. The system includes an automatic high-voltage shutdown for safety and user account management for access control.
Smart, User-Friendly Design
The device automatically selects the best capacitor and voltage based on the entered ignition energy value. The dust dispersion system ensures even dust distribution, and the 7-inch touchscreen shows real-time progress. The system also tracks electrode usage, warning when replacements are needed. A remote ignition control improves safety, and USB interfaces make data transfer easy.
Technical Specifications
- Operating Conditions: 5°C to 45°C, humidity <85% RH
- Charging Voltage: 0 to 15kV (no load)
- Electrode Material: 2mm tungsten
- Power Supply: 90VAC to 260VAC, 47Hz to 63Hz
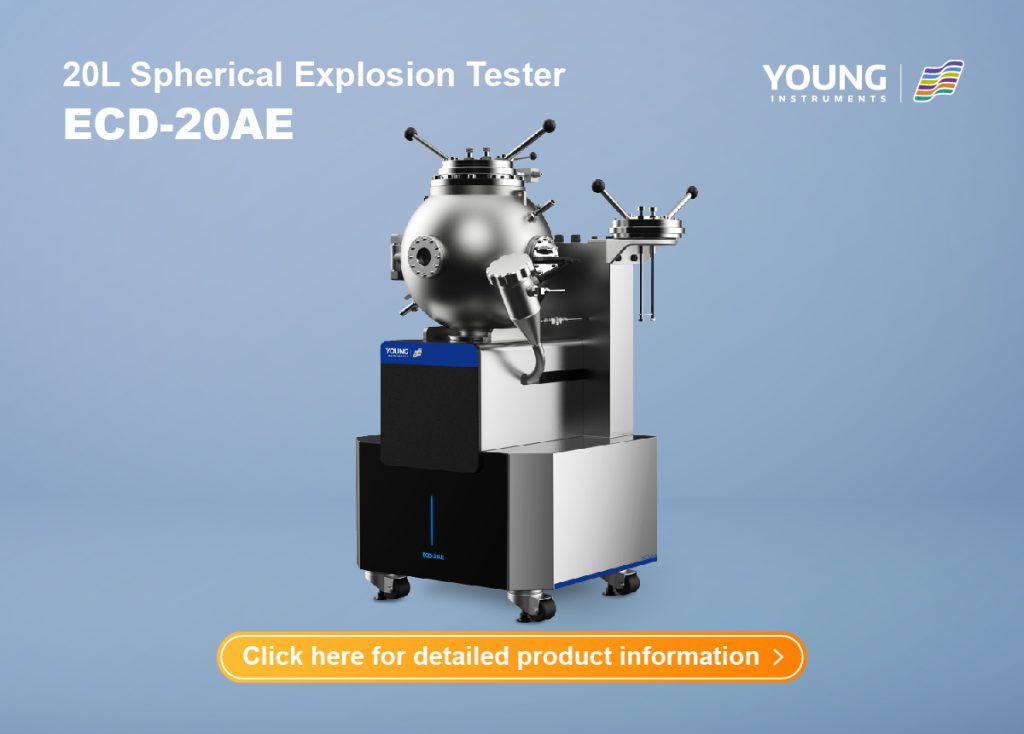
20L Spherical Explosion Tester ECD-20AE
Operation and Key Features
The ECD-20AE uses a 20L spherical stainless steel (316) vessel, pressure-resistant up to 3.0MPa at 25°C, with a water-circulating jacket to maintain stable temperatures up to 220°C. It safely tests dust, gas, and mixed explosions using chemical or electrostatic ignition. The system automatically manages cleaning, evacuation, and gas distribution, while real-time time-pressure data and a built-in dust dispersing mechanism ensure precise measurement of maximum explosion pressure, rate of pressure rise, and explosion index.
Safety, Standards, and Technical Precision
Compliant with international test protocols, the ECD-20AE supports working conditions from 5°C to 45°C (≤85% RH) and offers advanced pressure sensors (0-3.5MPa range with ±0.1% accuracy). The explosion pressure range extends to 10.0MPa with 0.001MPa resolution, and the temperature range reaches 1000°C with 0.01°C resolution. Remote monitoring and automated control protect operators, while the consistent sphere volume of 20L ensures repeatable results for testing materials such as aluminum, plastic, and sawdust.
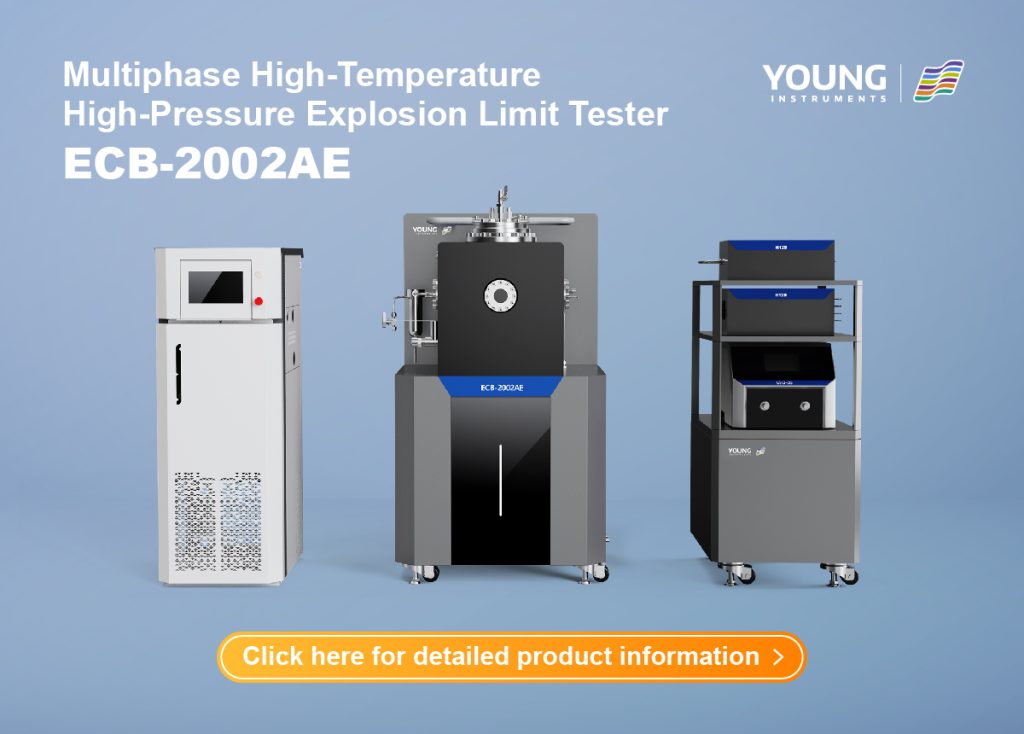
Multiphase High-Temperature High-Pressure Explosion Limit Tester
Advanced Explosion Characterization
The ECB-2002AE precisely determines explosion limits, minimum oxygen concentration, maximum explosion pressure, and pressure rise rate in compliance with ASTM E918, ASTM E2079, and EN1839. Its 316L stainless steel test chamber withstands up to 22.0 MPa, while maintaining stable operation in -5°C to 45°C environments (≤95% RH). A maximum gas pressure of 1 bar ±0.1% FS is supported for controlled mixing.
Precision, Flexibility, and Safety
The device features a 25.0 MPa explosion-proof sensor with ±1.0% FS linearity, alongside a 25 kHz sampling rate for accurate data. Gas mixing accuracy is ±0.2% FS at methane 0.254 SLM, and a stirrer running at 400 rpm ensures uniform concentration. Equipped with a vacuum pump, the system automatically handles vacuuming, mixing, stirring, and cleaning.
Technical Highlights
A jacketed temperature control (RT to 200°C) optimizes heat distribution for efficient testing. Modular construction and adjustable parameters allow customized experiments. Multiple safety interlocks protect laboratory staff, and 316L stainless steel construction resists corrosion. The ECB-2002AE is engineered for reliable, high-temperature high-pressure studies, combining precision measurement with robust safety features.

Explosion Range Tester
Operation and Scope
The HWP21-30SE measures the upper and lower flammability limits (UFL and LFL) of gases or flammable vapors. Testing is performed at 0 to 110 kPa (±0.1% FS) under adjustable temperatures from -10°C to 210°C with ±1°C accuracy. Data gathered helps evaluate fire and explosion risks across various applications.
Key Innovations
Available with 5L or 12L round glass vessels, the system ensures thorough mixing for better compatibility. It includes a compact heating/cooling module and monitors temperature, humidity, and atmospheric pressure in real time. The magnetic stirrer, remote start, and automatic ignition enable fully automated testing. All parameters can be configured, stored, and retrieved for reporting.
Safety Enhancements
A pressure relief door and spring-loaded compression setup provide secure pressure control. A built-in air circulation system balances temperatures, while automatic container cleaning removes combustion residues. The observation window features double-layer toughened glass with anti-fog protection, and a video monitoring system records each test.
Technical Highlights
Operating range is -5°C to 45°C (≤95% RH). Test objects include gases or vaporizable liquids/solids. Ambient temperature is measured from -10°C to 60°C, with humidity from 5% to 95% RH.
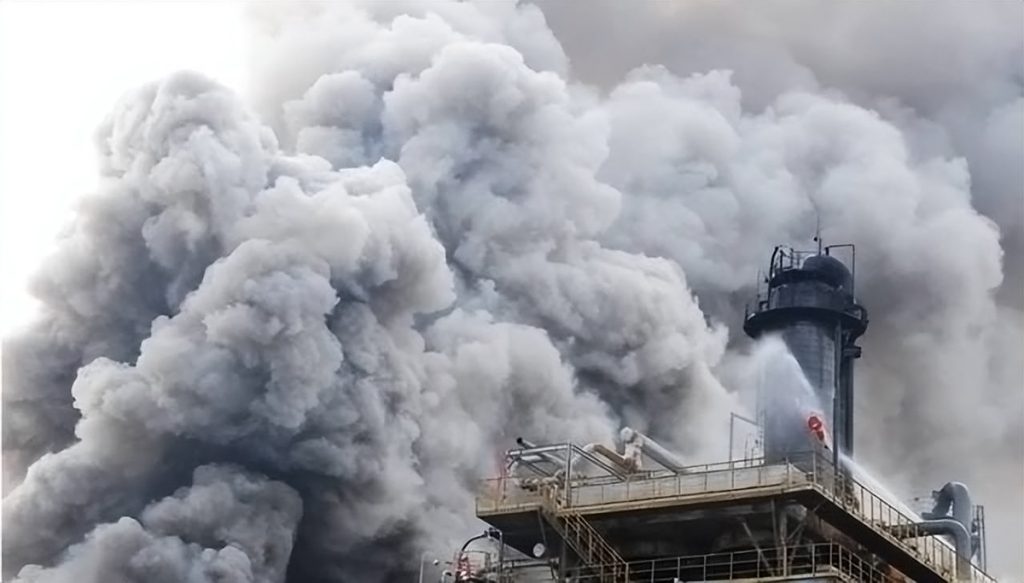
Enhancing Industrial Safety with Effective Management
Best Practices for Dust Control and Explosion Prevention
Dust control is important for safety in many industries. Keeping dust levels low reduces the risk of explosions. Use proper ventilation systems to remove dust from the air. Regular cleaning is also important to avoid dust buildup.
Safety Protocols and Emergency Response Planning
Having clear safety protocols is necessary for protecting workers. Plan for emergencies and make sure everyone knows what to do. Workers should be trained in using safety equipment. Regular drills help ensure that everyone is ready in case of an emergency.
The Impact of Testing on Workplace Safety Culture
Testing helps identify risks before they cause problems. Regular tests create a culture of safety. When employees see that safety is a priority, they are more likely to follow safety rules. Testing shows that the company cares about their safety.
Protect Your Workplace with Trusted Testing Instruments
Safeguard your operations from explosion risks with our reliable testing tools. Measure dust, gas, and pressure to identify potential hazards early. Prioritize safety, prevent accidents, and stay compliant. Contact us now to learn more and invest in a safer future!