The Charm of the Heat Flow Meter Method For Accurate Materials Testing
Thermal conductivity is a fundamental property of a material, unaffected by its shape or size. While multiple techniques are available for measuring thermal conductivity, no single method suits all materials and conditions universally. Factors such as material characteristics, testing standards, and environmental influences can impact results, making direct comparisons between different methods unreliable. Choosing the right testing approach is essential to obtain accurate and meaningful data.
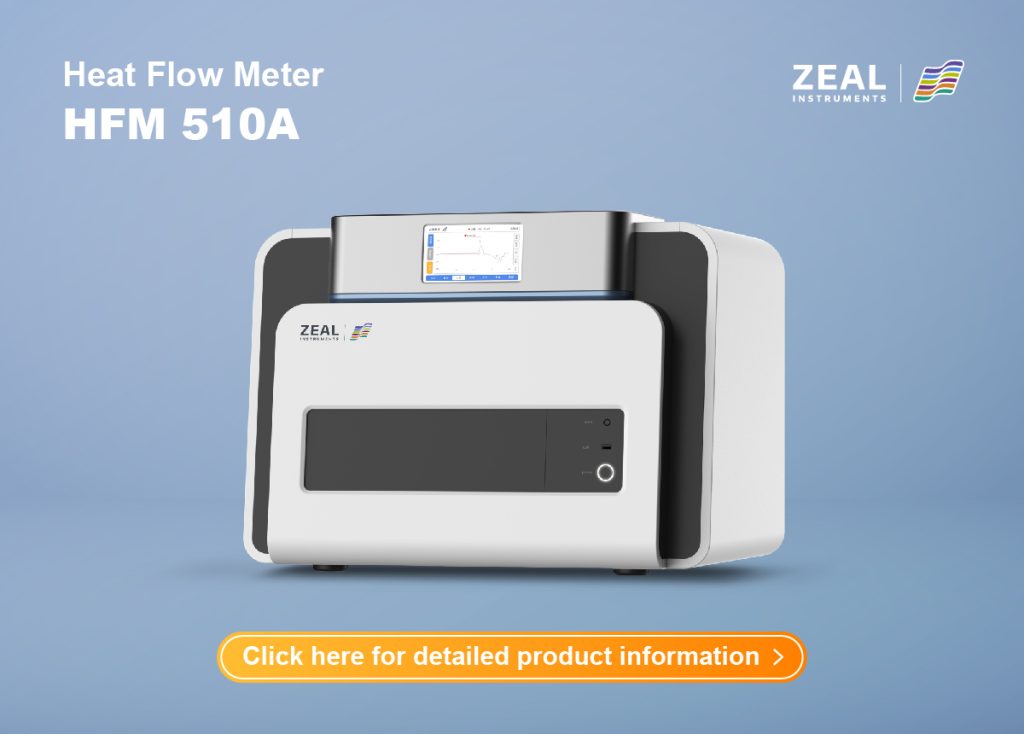
How the Heat Flow Meter Method Works
Basic Idea of the Heat Flow Meter Method
The Heat Flow Meter Method measures how well a material conducts heat. A sample with a fixed thickness is placed between two flat plates. One plate is heated, while the other stays cool. Heat moves from the hot plate through the sample to the cold plate. A heat sensor sits between the plates and the sample. It measures how much heat passes through the material.
Steps in the Testing Process
First, the hot and cold plates reach stable temperatures. Then, three key measurements are taken:
- The thickness of the sample
- The temperature of the top and bottom surfaces
- The heat flow through the sample
After collecting this data, a formula called Fourier’s Law is used. This equation helps calculate the material’s thermal conductivity. The test gives a clear idea of how well the material transfers heat. This method is simple, reliable, and widely used in material testing.
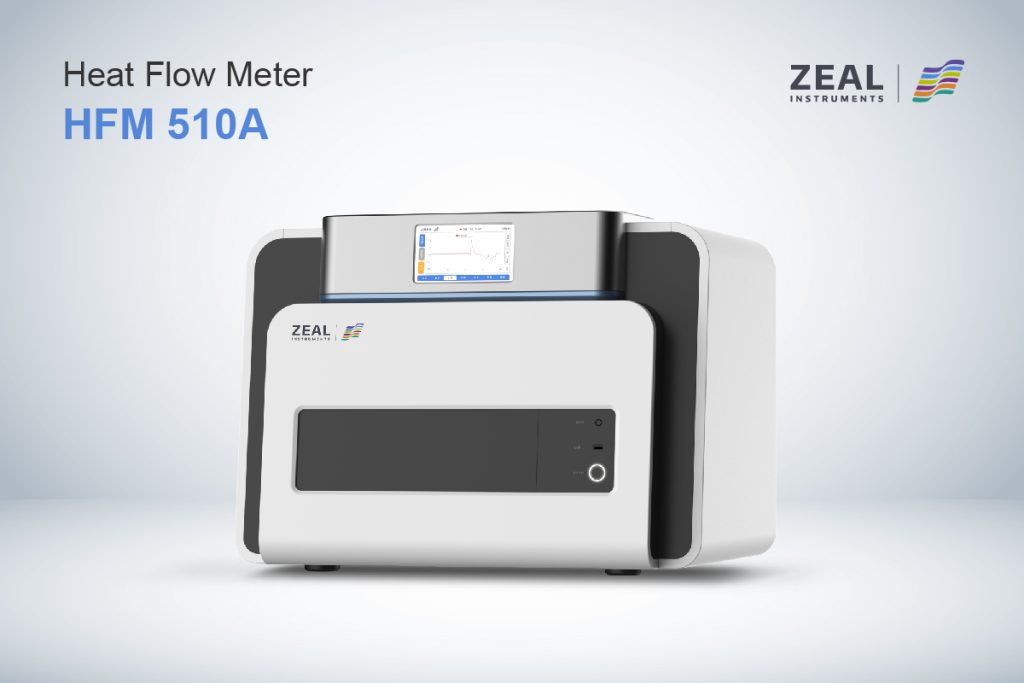
HFM 510A: Precision Thermal Conductivity Testing with the HFM Method
Versatile Material Testing for Multiple Industries
The HFM 510A complies with international standards such as GB/T 10295, ASTM C518, and ISO 8301, ensuring accurate thermal conductivity measurements. It supports a wide range of materials, including expanded and extruded polystyrene, PU rigid foam, mineral wool, foam glass, cork, aerogel, gypsum, and concrete. With a thermal conductivity range from 0.001 W/(m·K) to 1 W/(m·K) (expandable to 2 W/(m·K)), it is ideal for applications in construction, insulation, and advanced material research.
Advanced Automation for Precision and Efficiency
Designed for ease of use, the HFM 510A features automatic heating plate positioning, force load testing, and thickness measurement. The system includes a Peltier-controlled plate temperature range (-30°C to 90°C) and an external refrigeration cooling system for stable operation. An automatic nitrogen purging system ensures sample drying, improving test accuracy. With more than 10 temperature set points, users can conduct highly precise experiments.
User-Friendly Software and Smart Data Management
The high-definition touchscreen display provides an intuitive user interface. Users can access custom data storage, historical test records, and offline operation modes. The built-in industrial computer supports peripheral connections (mouse, keyboard, and printer), eliminating the need for external devices.
Fast, Accurate, and Expandable Testing Capabilities
With dual heat flow sensors and independently controlled upper and lower plates, the HFM 510A adapts to uneven sample surfaces, ensuring high-precision results. It supports samples up to 300mm (L) × 300mm (W) × 100mm (H) with a measurement resolution of 0.02mm. The thermal resistance range extends from 0.1 m²K/W to 8 m²K/W, with ±1% to 2% accuracy and 0.5% repeatability. A variable load force of 21 kPa (1930N) ensures reliable sample contact.
With real-time data collection, automated reporting, and expandable configurations, the HFM 510A is a powerful, efficient, and user-friendly solution for thermal conductivity testing.
Comparing HFM with Other Thermal Conductivity Methods
Guarded Hot Plate vs. Heat Flow Meter
The Guarded Hot Plate (GHP) method and the Heat Flow Meter (HFM) method are both used to measure thermal conductivity. However, they work differently. The GHP method uses a heated plate between two samples of the same material. It measures heat transfer under steady-state conditions. This method is accurate, but it takes a long time and requires strict testing conditions.
The HFM method also uses a heated plate but measures heat flow through a single sample. It is faster and easier to use. The equipment is more compact and requires less energy. Because of this, HFM is more suitable for routine testing in laboratories and industries.
Transient vs. Steady-State Methods
Thermal conductivity methods are divided into transient methods and steady-state methods. Steady-state methods, such as GHP and HFM, measure heat transfer after the temperature becomes stable. These methods take longer but provide highly accurate results.
On the other hand, transient methods, like the Hot Wire Method and Laser Flash Analysis, measure heat transfer over a short period. These methods work quickly and are useful for materials with very high or very low thermal conductivity. However, they often require more expensive equipment and complex calculations.
Advantages of HFM for Routine Testing
The Heat Flow Meter (HFM) method has many benefits for routine testing. It is easy to use and does not require highly trained operators. It provides fast and repeatable results. The automatic functions reduce human error. Unlike the GHP method, it does not need two identical samples, which makes sample preparation easier.
HFM also works with a wide range of materials, from insulation boards to construction materials. It is suitable for industries that need regular thermal conductivity testing, such as construction, aerospace, and manufacturing. Because it balances speed, accuracy, and ease of use, it is one of the best methods for routine material testing.
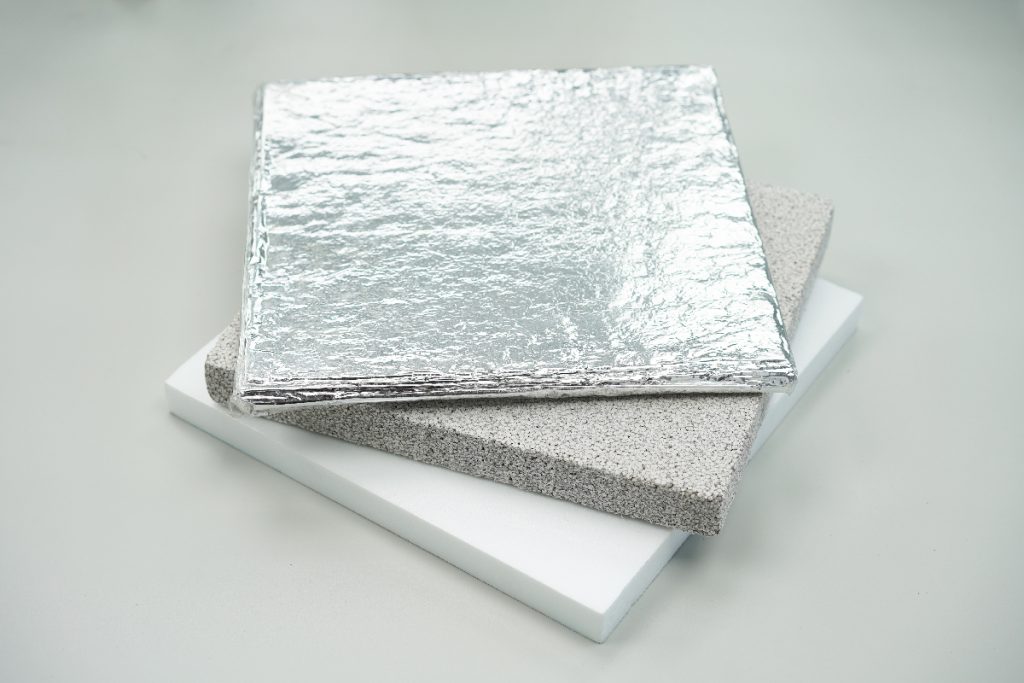
Applications of the Heat Flow Meter Method
Measuring Thermal Conductivity of Insulating Materials
Insulating materials have a thermal conductivity of less than 0.12 W/mK. These materials are often lightweight, porous, or fibrous. They work by trapping air, which helps slow down heat transfer. Because of this, they are commonly used in buildings, industrial equipment, and household appliances. Proper insulation reduces energy loss and improves temperature control.
The Heat Flow Meter (HFM) Method is widely used to measure the thermal conductivity of these materials. It provides accurate and consistent results. Many industries rely on this method to ensure their products meet energy efficiency standards. Materials like expanded polystyrene, mineral wool, foam glass, and aerogels are often tested with HFM. This helps manufacturers create better insulation solutions.
Importance in Construction and Industrial Applications
The construction industry uses insulation to improve energy efficiency in homes, offices, and factories. Good insulation reduces heating and cooling costs. It also makes buildings more comfortable by maintaining a stable indoor temperature. The HFM Method helps builders and engineers choose the right materials for walls, roofs, and floors.
Industrial sectors also depend on insulation. Factories, pipelines, and refrigeration systems need insulation to control heat flow. Without proper insulation, energy loss increases, leading to higher costs. The HFM Method ensures that insulation materials perform as expected. This makes it an essential tool in energy management and material testing.
Improve Energy Efficiency with the HFM Method
The Heat Flow Meter (HFM) Method tests insulation materials. It gives accurate and reliable results. It helps industries meet energy-saving standards. Many materials, like polystyrene, mineral wool, and foam glass, are tested with HFM. This ensures high-quality insulation.
The HFM Method is useful in construction and industry. It helps builders choose the right insulation. Factories need it to control heat flow. Better insulation means lower costs and better efficiency. Contact us now!